Mention Project Critical Chain to any project professional and chances are you’ll get a blank stare. You may even be questioned back, “Project Critical Chain? Don’t you mean Project Critical Path?”. Mention Theory of Constraints (ToC) and the confusion is complete.
Well, it shouldn’t be that way. You may be familiar with these methodologies but struggle with explaining the concept to your colleagues or boss. Or you may be completely new to the terminologies and can’t find a simple reference. Well, then this blog post is for you!
In this blog post you’ll learn the five concepts associated with Theory of Constraints (ToC) and Critical Chain (CC) to Real Projects, and how this would change the project’s course from failure to success.
We’ll review together a real-world project example that was impacted by multiple types of constraints, and how the proper implementation of the Critical Chain Project Management (CCPM) would have changed its outcome.
The Theory of Constraints (ToC) Measurement and Project Critical Chain Steps
Eliyahu M. Goldratt, the Godfather of the Theory of Constraints (ToC), was the one that simplified it through his best-selling business novel “The Goal” into five simple steps to be followed for pursuing continuous improvement.
While these steps were applied on a production facility environment, it has been widely proven that the implementation of the ToC steps on a project’s environment could bring in huge rewards for any organization, provided that the same three primary measurements that Dr. Goldratt identified as being the core and the sole performance indicators of any business wellbeing are the ones implemented on the project(s) as well.
This was when Goldratt’s Critical Chain (CC) theory–and business novel–was born to help simplify the ToC application within any project’s planning and execution phases.
The measurements cited by Dr. Goldratt are Throughput, Inventory, and Operating expense. According to Dirgo, Robert in his book “Look Forward Beyond Lean And Six Sigma”, those measurements could be defined as follows (p.104) and is illustrated in Fig. 1 below.
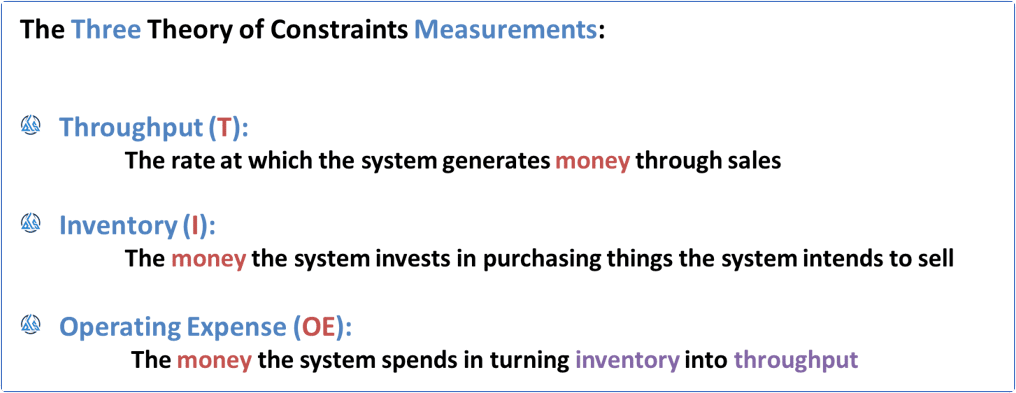
Figure 1: The Three Theory of Constraints Measurements
As you see, those definitions are geared towards production and sales, and they are not easily transferred to the project management world.
However, if we want to relate them to three typical basic metrics of project health measurement, we could find a lot of resemblance between them and the very common ones we use within the Earned Valve Management (EVM) framework (Fig. 2 below).
Therefore, Throughput equates to Earned Value (EV), Inventory equates to Planned Value (PV), and Operating expense equates to Actual Cost (AC).
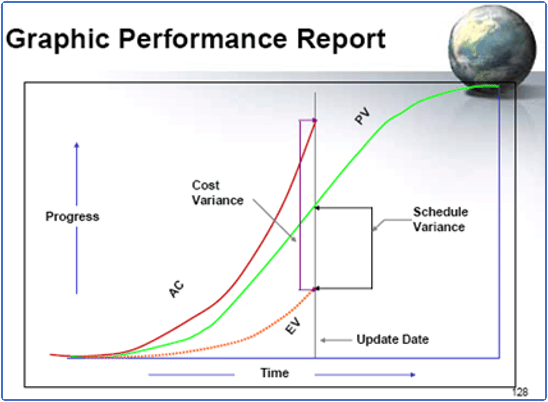
Figure 2: Earned Value Management from PMI.org
Now, let’s switch gear and talk about the ToC/ Critical Chain steps that Goldratt suggested to be followed throughout the project for a successful Critical Chain Project Management (CCPM) implementation. We illustrate the five steps in Fig. 3 below and further outline each step.
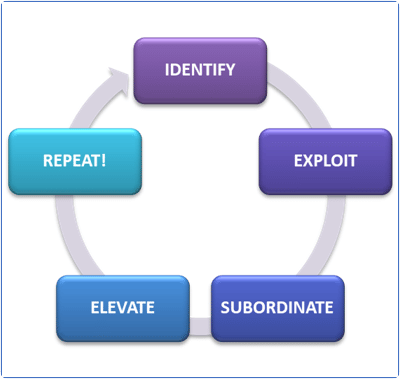
Figure 3: The Five Theory of Constraints Focus Steps for Project Critical Chain
Project Critical Chain Step 1: Identify the Constraint
A project constraint could be anything that is continuously hindering the project’s Earned Value (EV) from meeting the PV. It could be an internal resource (person, equipment, machine, material, money, or a combination of all), or an external one (supplier, contractor, consultant, vendor, third party inspector, agency, regulation, permit, etc.).
Generally, there are multiple project constraints at the same time, but the idea here is to identify the most critical one, and the Critical Path schedule is usually the best place to start looking for it, if it is properly put together, to begin with!
Project Critical Chain Step 2: Exploit the Constraint
The word Exploit means “to use something in a way that helps you”. While the approach towards how to do that will mainly depend on the type of the identified constraint, the main objective remains the same; Maximizing the constraints’ contribution to the Throughput (Earned Value) of the project.
Project Critical Chain Step 3: Subordinate Everything Else to the Constraint
This is widely referred to as “setting the drumbeat”, where the identified constraint is the Drum, and the resource/person behind it is the Drummer.
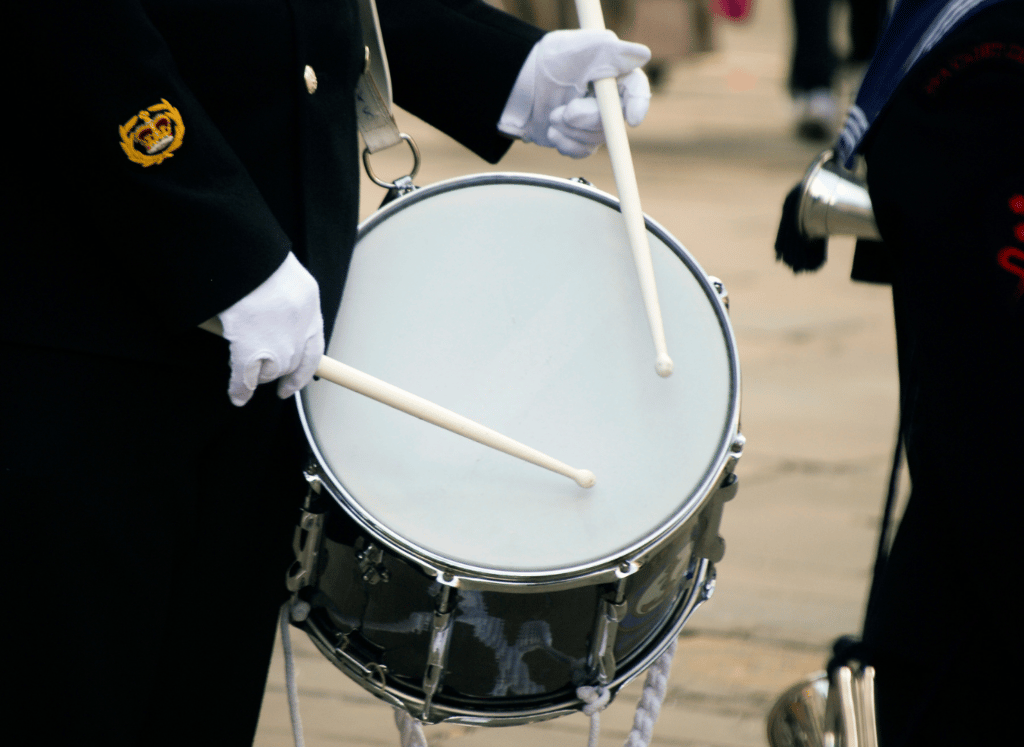
Figure 4: Setting the Drumbeat in the Project Critical Chain
We need to make sure that we reach an equilibrium point within the project’s EV analysis that we are not significantly outpacing the target PV, and while doing that we are exhausting the other parts of the project to keep up, resulting in unnecessary additional AC.
For example, in Fig. 5 below a pipe-trenching machine within a pipeline construction project identified as the constraint is now working at full capacity that is above the baseline targets (PV) means that the trench-lining crews are now required to work overtime to keep up with the machine rate, resulting into significant overtime expenses (AC) for the project.
This results in the project’s high Schedule Performance Index (SPI= EV/PV) but a sharp drop in its Cost Performance Index (CPI= EV/AC).
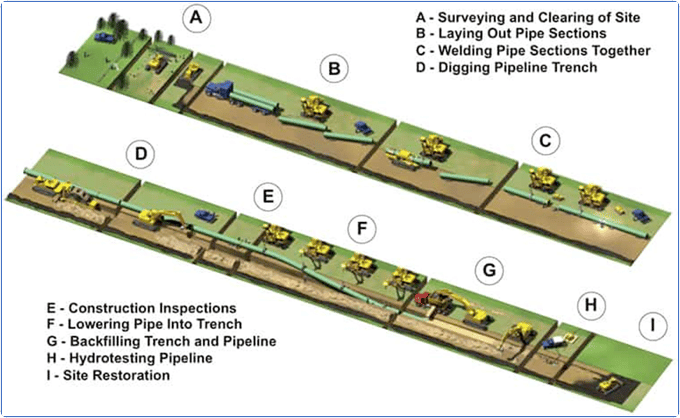
Figure 5: Applying Project Critical Chain in a Pipeline Construction Project
Project Critical Chain Step 4: Elevate the Constraint
Once we achieve the desired equilibrium within a project, it is time now to look into the critical path(s) where the constraint(s) are acting like the drums and trying to find ways to increase the throughput of the whole path, not just the constraint.
It is as if you are holding the EV curve from the constraint and pulling it up, and while you are doing so you are actually “elevating” the whole CC curve up!
This step will usually take the longest time and largest effort to implement since it involves not only finding ways to increase the constraints’ throughput but also all the other steps, tasks, and activities that precedes or succeeds it within the project’s Critical Path.
The expected result out of this step is to eliminate the constraint’s impact on the project’s Earned Value altogether.
Project Critical Chain Step 5: Go Back to Step 1 and Identify the Constraint
Let’s face it.
There will be not a single instance where we can say that we have eliminated all the project’s constraints! Every time we elevate a constraint, the next-in-line will pop up as the new project’s constraint.
This is now why the Theory of Constraints (ToC), according to Dirgo, is considered one of the Big Three Continuous Improvement Tools, alongside Six Sigma and Lean, because it creates an endless loop of eliminating constraints in our pursuit for perfection
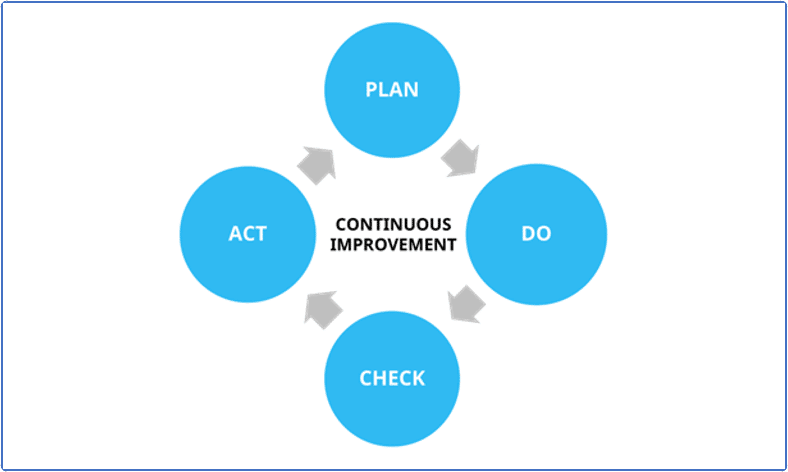
Figure 6: Continuous Improvement – Essential to the Success of Project Critical Chain
Obviously, the more constraints we eliminate the harder it will become to overcome the next one, so it will boil down at this stage to other organizational factors that would guide us on the course to take.
Following these steps will help to nail down the project Critical Chain; The longest chain of steps that have a resource dependency. That is, of course, after we’ve reached the point where we have repeated the steps until we confidently achieved a practical & manageable CC.
Fig. 7 and Fig. 8 below summarizes the difference between the project Critical Chain and critical path.
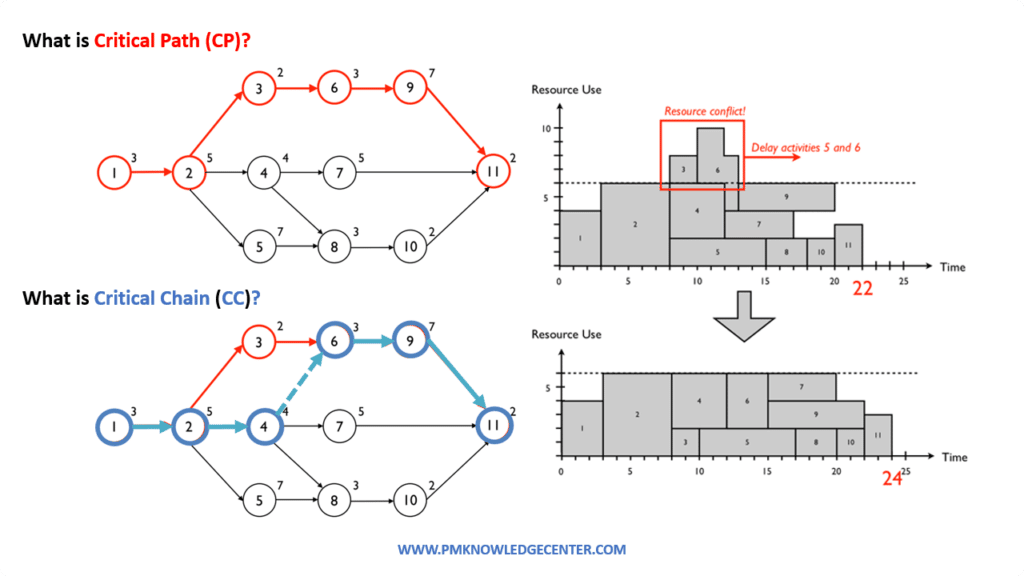
Figure 7: Project Critical Path versus Project Critical Chain
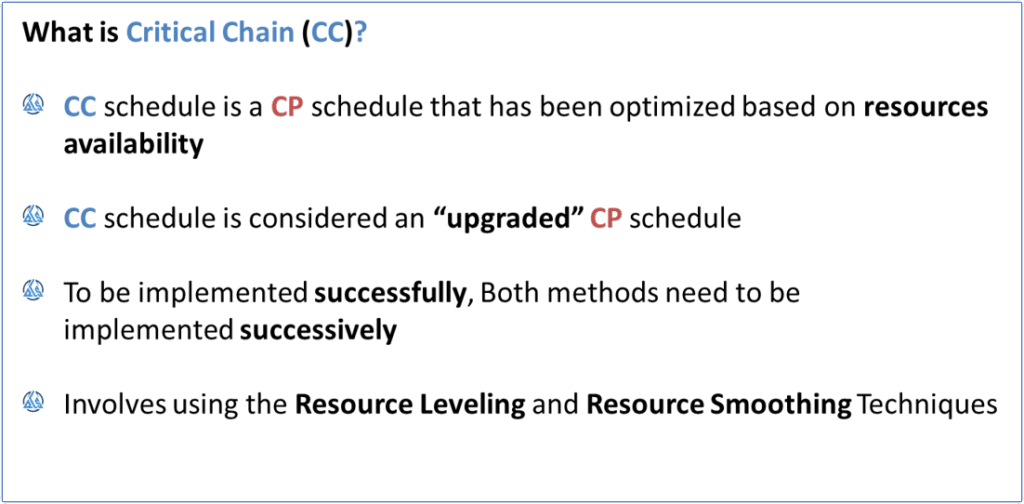
Figure 8: Key Points of the Project Critical Chain
Theory of Constraints between Organizations and Projects
When we look at implementing the Theory of Constraints (ToC) within our projects, we can’t ignore the fact that the organization that is carrying the project also needs to adopt the ToC steps across all its aspects in order to achieve the desired goal behind its existence in the first place, i.e. to make money. Fig. 9 below puts the ultimate goal of any business into perspective.
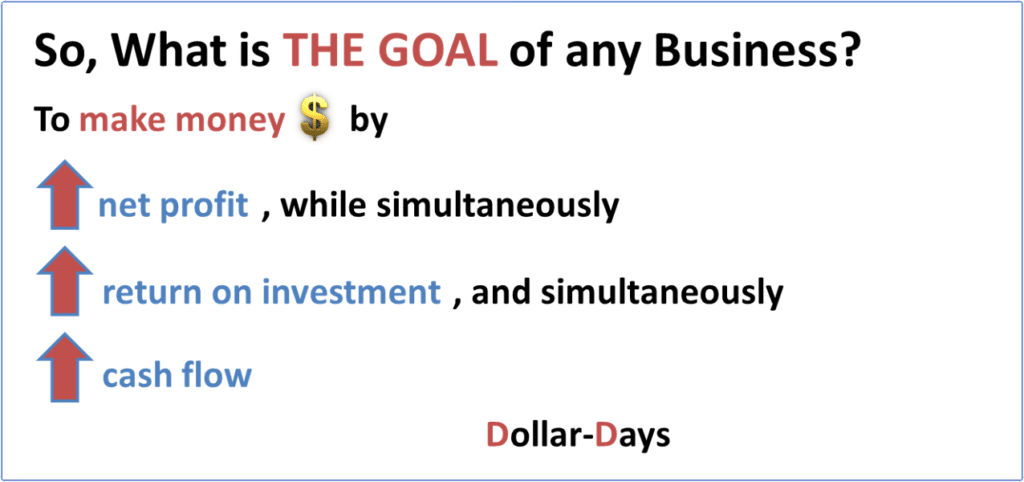
Figure 9: At the End of the Day the Project Critical Chain Must Align to The Business Goal
While Theory of Constraints (ToC) can partially work in isolation within a single project, its full potential lies in the full implementation of it. Dirgo mentioned this in his book as referenced here below (p.95):
“Theory of Constraints requires an intimate association with the business processes being improved and, contrastingly, a concurrent understanding of the global elements that contribute to the desired outcome. It forces you to think and to look at your business in ways you never may have done before. It fosters revolutionary change that transforms a company by providing a methodology for enabling its employees to focus their efforts on a common goal.”
The Project Critical Chain Measurement
Figure 10: Significant Quote Regarding Project Critical Chain Project Management
“Tell me how you measure me, and I’ll tell you how I’ll behave” is considered a significant quote by Dr. Goldratt when it comes to Critical Chain Project Management (CCPM). Organizations rely on the way they measure progress and efficiency to assess their success, plan their resources, and take significant project decisions.
This brings us to the next important point; how can we properly measure operations and monitor progress of a project when it comes to implementing the Critical Chain Project Management (CCPM)? Most–if not all–organizations use a management philosophy that implies that any local improvement automatically translates into an improvement of the organization, easily referred to as the “Cost World”.
On the other end, Critical Chain Project Management (CCPM) advocates that in order to achieve the desired outcome we need to measure our progress and efficiency in accordance with the “Throughput World”, a philosophy that focuses on the critical chain links as well as the linkages in between them with an emphasis on finding the Critical Chain (CC) weakest link (Constraint) and continue to strengthen and monitor it.
Goldratt used the “tons-per-hour” as an excellent example of how a prime operational measurement has been–and still is–dominating the steel fabrication industry and continuing to influence the people’s behavior in trying to maximize their performance by producing heavier and easier items at the expense of lighter and more complicated ones. I have experienced the same attitude in a major bridge construction project as it had a huge structural steel fabrication and installation scope component. I will try to reflect on how the Critical Chain Project Management (CCPM) could have been used to resolve the delays that this project execution experienced.
Real-World Project Critical Chain Case Study - Sheikh Zayed Bridge
Let’s review a project example that had one or more constraint(s) hindering its Critical Chain and evaluate what could have been the outcome if the appropriate steps would have been implemented through it.
The Sheikh Zayed Bridge (SZB) project in Abu Dhabi, UAE started construction in 2003 and was supposed to take only 3 years. By 2010, the project was only 87% complete and the anticipated completion date was July 2011, five full years after the original baseline one!
What happened in those 8 years of construction? And why did the project experience such an undesirable outcome that resulted in the original contractor’s removal from site and the client bringing in another contractor to assume responsibility and control on the project?
The answer lies in a list of constraints, internal and external, that hindered–and at some point halted–the project’s progress from moving forward. Those constraints were mainly linked to a significant element of the bridge, the three massive Structural Steel Arches seen in Fig. 11 below.
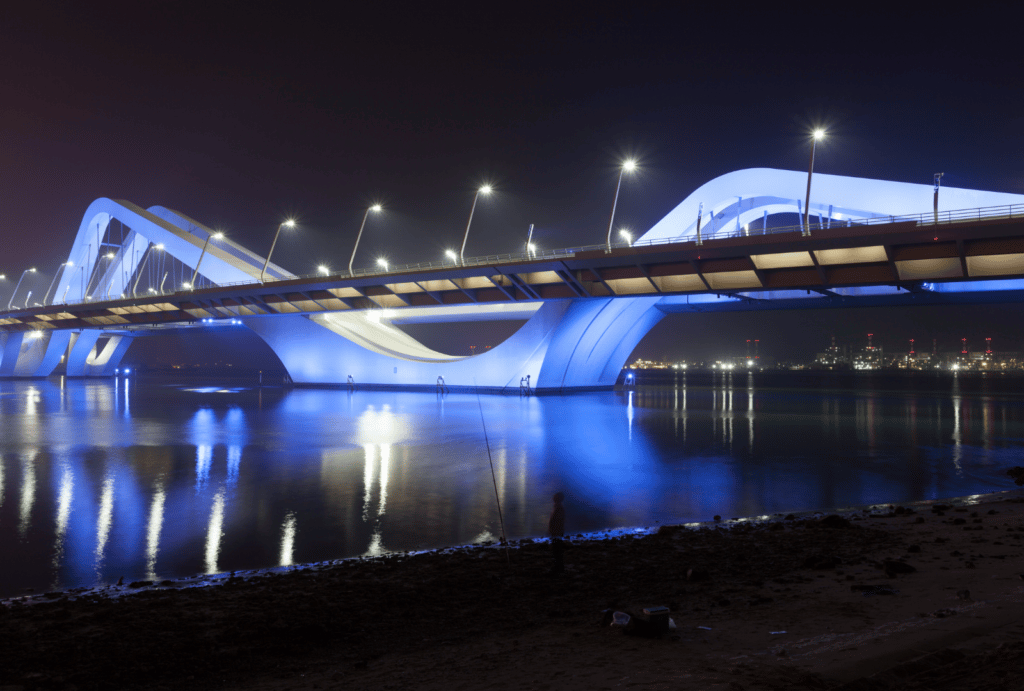
Figure 11: Sheikh Zayed Bridge – Landmark Project Applying Project Critical Chain
Those steel arches are the ones holding the bridge concrete deck crossing across the waterway and are required to be in place before the majority of construction works advances.
The constraints related to the arches involve multiple External and Internal ones. While each category would have more than one significant constraint impacting the schedule’s critical path at one time, I will list here below the main highlight of each category that had the biggest impact on the project’s critical chain throughout the project’s course as well as reflecting on how those constraints were linked to a major resource element that was proven to need proper management by providing the appropriate Feeding and Resource Buffers in order to mitigate its impact on the project’s critical chain.
External Constraint Within the Project Critical Chain:
The steel arches fabrication was awarded to a steel fabricator overseas, with no appropriate supervision and oversight from the contractor’s side on their progress. The result was continuing slippage on target completion and shipment dates with no recovery plan to bring it back on track.
Going back to Goldratt’s example of steel production, it doesn’t take long before you realize that the same exact behavior was the reason behind this outcome. The steel fabricator was using the same metrics (tons-per-hour) to measure their production and efficiency rate rather than focusing on finishing the structural steel elements in the most optimized way that would ensure a fast fabrication and delivery in accordance with the construction sequence.
Hence, supervising foremen in the fabrication yard were pulling the heavy steel elements parts for fabrication out of sequence in order to reach their target production rate earlier into the month, then they would switch to smaller sized elements production while keeping another batch of larger steel elements on the queue till next month.
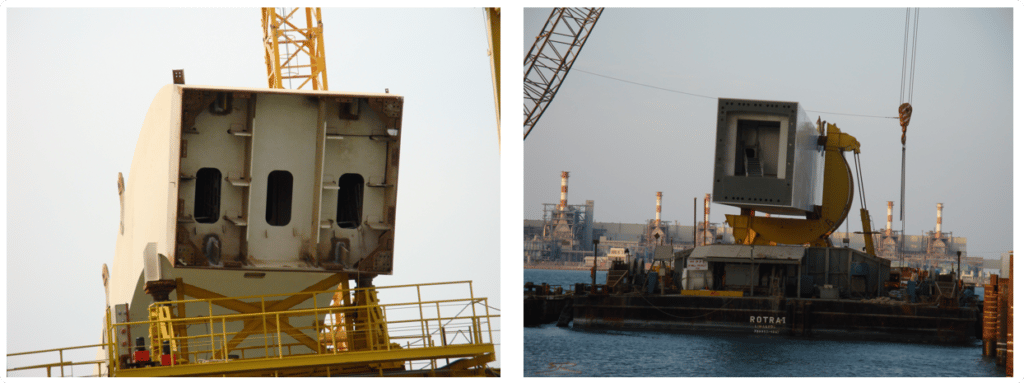
Figure 12: Out-of-Sequence Fabrication – External Constraint Within the Project Critical Chain
That way they are guaranteeing that they would reach their targeted tons-per-hour production rate every month without a hassle and ignoring following any proper sequence that would ensure faster delivery and mess with their sacred production plan!
Producing heavy and fast items at the expense of lighter and slower ones was all that they were thinking about, and all sorts of fake excuses were given to the contractor that there was no other way to do it other than what they were doing, and the lack of proper supervision at the beginning helped them to get away with that.
By the time the contractor figured out the real reason behind the delays and sent a team to exploit this constraint it was already too late. The damage was imminent.
Internal Constraint Within the Project Critical Chain:
There was no market availability of a crane’s capacity that is capable of lifting and holding such massive steel arches elements in place until they are welded together while the crane is positioned on a floating barge! (The biggest steel arch is composed of 6 heavy elements of 500 tons each).
Hence, the process required a sophisticated temporary support & strand jack lifting system that is capable of lifting and positioning at least 600 tons at a time. This system was designed and built on several temporary piles that were removed and reinstalled to complete the three arches installation and welding process successively, as seen in Fig. 13 below.
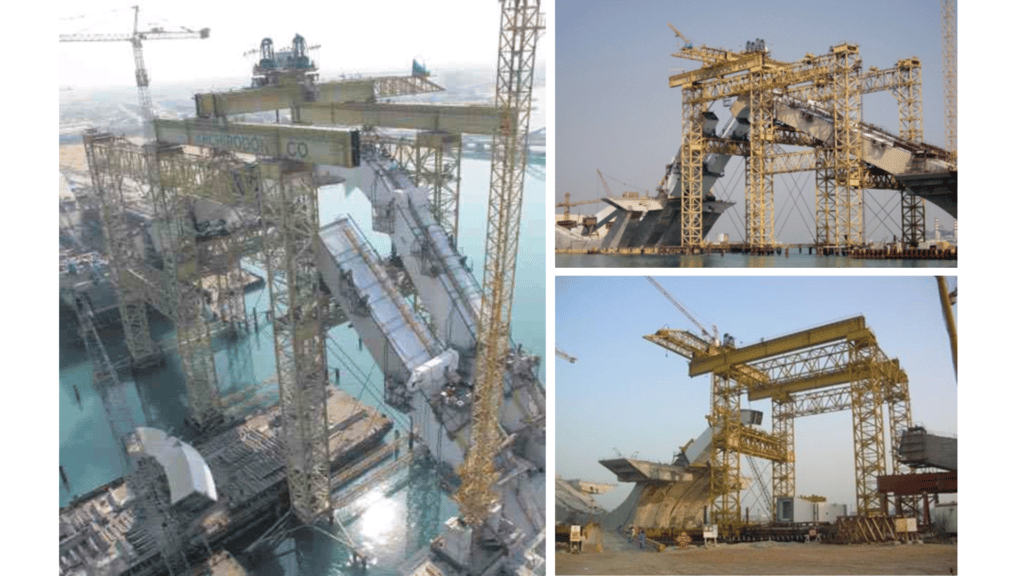
Figure 13: Steel Arches Installation – Internal Constraint Within the Project Critical Chain
From Project Critical Path to Project Critical Chain
While the steel arches fabrication (External constraint) and steel arches lifting (Internal constraint) formed the schedule’s critical path, the real project critical chain was not truly highlighted until the team was able to discover that the steel arches welding crews were the constrained resource that the project critical chain is really going through.
These two crews were formed from a group of highly trained and experienced structural steel welders that required special training and certifications to be able to weld such sophisticated steel junctions through upside-down positions while being elevated, as seen in Fig. 14 below.
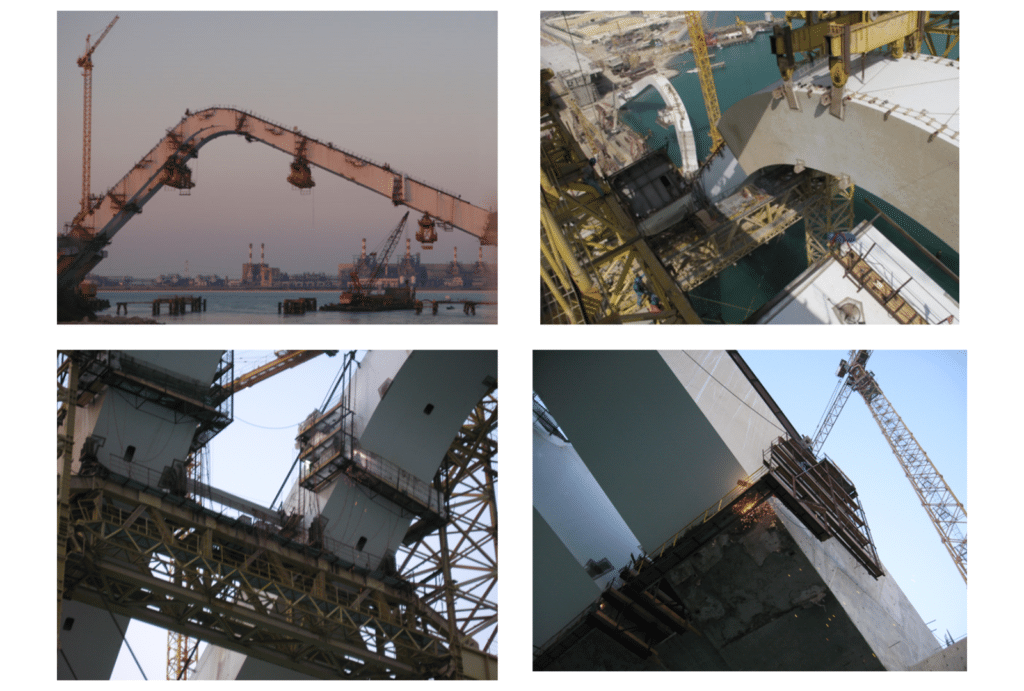
Figure 14: Steel Arches Welding – Within the Project Critical Path or Project Critical Chain?
This was the real project Critical Chain constraint! Even if all the arches were to be installed in the perfect sequence and timing, these two welding crews would have had to go through each junction one after the other, working in parallel, to complete its welding before moving to the next one.
All the remainder of the project activities (Critical path or not) would need to subordinate to the welding crews’ production rate (drumbeat) before thinking of elevating it.
Exploit, Subordinate, Elevate, Repeat!
It took the project management team a long time before realizing that the conventional ways of approaching the schedule recovery options (like overtime, additional crews, more equipment, etc.) would not work, and more breakthrough solutions are required. Once the constraints were identified, exploited, and elevated, the project finally started to gain throughput, and the recovery path started to take shape, although very late into the game, unfortunately.
Exploiting and Elevating the External Constraint:
The team decided to remove the fabrication scope of one of the three steel arches (the smallest one of them) from the overseas-based fabricator and appointed another local structural steel fabrication firm to complete the job.
This involved shipping the raw material from overseas to the local fabricator to speed up the process and appointing local inspectors both at home and abroad to supervise the job on a daily basis. Now the overseas fabricator had more resources focused on less amount of scope elements, resulting in better workmanship quality, fewer rework instances, and more achievable and predictable shipment dates.
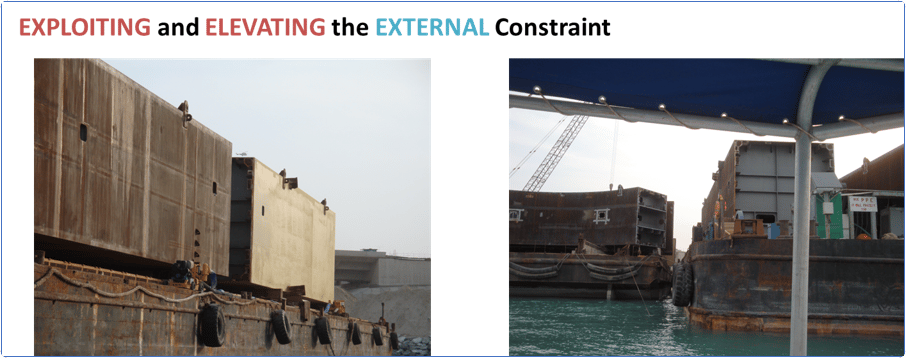
Figure 15: Exploiting and Elevating the Project Critical Chain External Constraint
By providing both fabricators with the exact required construction sequence and asking them to work backward for their fabrication priority sequence without paying attention to their tons-per-hours rate, with strict supervision, they were able to significantly enhance their delivery dates and ship the steel arches segments in the proper construction sequence just-in-time for the lifting operations to start, avoiding double handling, occupying the barges, cranes, and handling crews unnecessarily until lifting operations could start.
Subordinating and Elevating the Internal Constraint:
Moving one of the structural steel arches from the overseas-based facility to a local fabricator’s one resulted in a better-expedited delivery date for this arch’s elements than forecasted earlier.
This meant that the installation schedule would need to follow suit, or the required project’s throughput would not be achieved all the way across the project Critical Chain. It also reaffirmed the fact that there will always be another constraint in line once the first one is exploited and elevated.
The construction team conducted huge research and came up with a break-through idea to remove this marina arch’s elements from the Critical Chain path that is using the temporary support and strand jack lifting system by building a temporary cofferdam only in the waterway under where the arch needs to be installed.
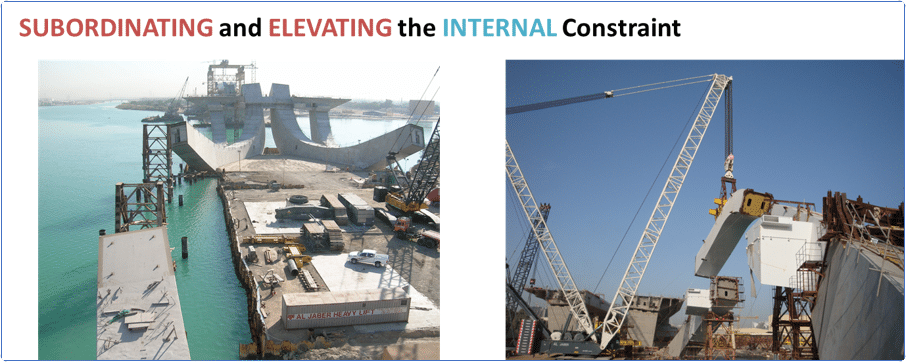
Fig. 16 – Subordinating and Elevating the Project Critical Chain Internal Constraint
The team also opted to use a world record-breaker 1,600 ton crawler crane (Fig. 17 below) to install it instead. This provided the required buffer for any delays on the Critical Chain.
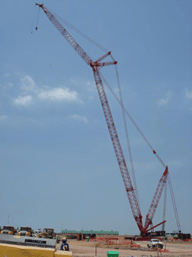
Figure 17: Using a 1,600 ton Crawler Crane to Provide Buffer Within The Project Critical Chain
This methodology, while it had an additional cost upfront due to the additional cofferdam building and crane rental costs, resulted in these costs being balanced at the end with the savings from reducing the delay penalties, crews’ overtime cost, and the earlier release of the expensive strand jack lifting system back to the supplier, to name a few!
Leveling the Constrained Resources
If the team would have rushed earlier and hired additional expensive welding crews to help speed the welding process, thinking that this could be the only way to expedite the project, these crews would have sat idle for weeks racking high pay-rate with nothing to do!
Instead, the team leveled the usage of the two welding crews between the installation of the arches within the three locations through using the buffer time that was created from breaking the temporary support and strand jack lifting system sequence-dependency and using a temporary cofferdam and crawler crane approach in one of the steel arches installation locations.
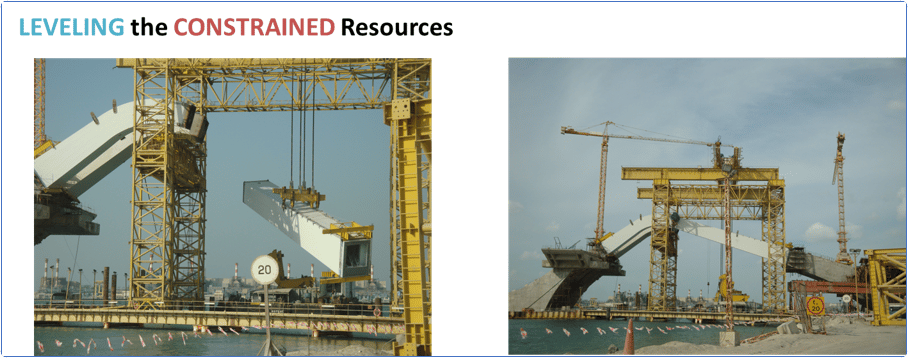
Figure 18: Leveling the Constrained Resources in the Project Critical Chain
This provided the time bucket required to insert some feeding buffer ahead of the welding activities when the crew is moving from welding one junction to the next.
By the time the two welding crews are completing the welding on the second installation site (using the crawler crane) the temporary support and strand jack lifting system is being moved from the first location and reassembled on the third location, eliminating any downtime for the welding crew and creating some buffer to use should one of the junction welding activities took longer than estimated.
Final Thoughts on the Theory of Constraints and Project Critical Chain
While projects facing a number of constraints, whether they are external or internal, throughout the project’s lifecycle, is something that is inevitable, the approach that the project team would take towards those constraints can either make or break the project’s outcome.
Theory of Constraints (ToC) has proven, time over time, that it is a systematic, yet simple, approach to tackle the constraints impact one after the other on the project’s Throughput (Earned Value) without outpacing the project’s Inventory (Planned Value) or overburdening the project’s Operating Expense (Actual Cost).
Theory of Constraints (ToC) steps needed to be followed in order and continue to be re-implemented over and over in the team’s pursuit for perfection. Continues Improvement is the backbone of ToC and an organization can only reap its full reward only when it is implemented across the whole company system, not just on a local basis in one project or function.
As mentioned earlier, it’s only feasible to apply the Theory of Constraints (ToC) and Critical Chain (CC) methodology if there is currently a true and reliable critical path for the project. Only then can we optimize and upgrade the project critical path to the Project Critical Chain using leveling/smoothing and buffers.
Would you need some help on developing a reliable critical path in your project? To get the foundations of developing project schedule the right way? Then join us in our upcoming Project Scheduling Blueprint training!
Learn how not only to build a robust and effective project schedule but understand the project planning and scheduling foundations and the principles behind CPM (critical path method).
If this is for you, take this opportunity now and we can’t wait to have you join us!
References:
[1]- Goldratt, E., Cox, J. (2014). The Goal: A Process of Ongoing Improvement, 4th Ed. The North River Press.
[2]- Goldratt, E., Cox, J. (1997). Critical Chain. The North River Press.
[3]- Dirgo, Robert. (2006). Look Forward Beyond Lean and Six Sigma: A Self-Perpetuating Enterprise Improvement Method. Chapter 5. J. Ross Publishing.
[4]- Harvey A. Levine. (2005). Project Portfolio Management, Section Eight: PPM for Theory of Constraint Advocates. Jossey-Bass.
[5]- Philip Marris. Jun 6, 2017. Theory of Constraints crash course by Philip Marris. MarrisConsulting. Youtube Video.
[6]- Constructing an Icon. Sheikh Zayed Bridge. Roads Bridges.com.
[7]- New builder to finish construction on Sheikh Zayed Bridge. The National News.
[8]- Sheikh Zayed Bridge may open in October as new contractors arrive. The National News.
[9]- Billion-dirham bridge: An exclusive tour of Abu Dhabi’s newest bridge with contractors Sixco.
[10]- Sheikh Zayed Bridge by Zaha Hadid Architects.
About the Author:
Ihab is originally from Cairo, Egypt where he completed his bachelor’s degree in Civil Engineering, and since then he has been working in the field of Project Controls and Project Management. He has been a leading professional in multiple international companies in the UAE and Canada a for a variety of projects and industries, including structural steel fabrication, mega-bridges construction, LNG marine terminals, hydrocarbons extraction, processing & transportation, as well as mining, pipelines, terminals, and utilities projects.
In in addition to his PMP, PfMP, DASM, and CCP certificates, he has recently earned his Master’s degree in Project Management with honors. He is also a certified PMP Trainer with PMI and currently working as a Project Controls Consultant and leading multiple major PMO setting up related endeavors.
Project Management has been his passion and profession for his entire career, and he enjoys overcoming its challenges day in, day out!
Connect with Ihab via LinkedIn or pyramidpmo.com